BE the Solution
A global Client tasked Brindley Engineering (BE) to expand their refinery capacity by upgrading their fractionation unit and interesterification tanks at a brownfield site located in the Midwest. Prior to BE’s involvement, the original project scope included a third-party engineered and designed turnkey system that included the addition of a new building to accommodate the required piping, mechanical, electrical instrumentation and controls equipment.
The Challenge
As part of the design evolution of the original scope, the overall process scope was decreased, the addition of a new building was deemed not applicable, and as a result, the Client enlisted BE to perform basic and detailed engineering and design activities to implement portions of the previously engineered and designed systems into their existing buildings and tank farm. During basic and detailed engineering activities, BE’s team of electrical control and instrumentation engineers deployed standardized BE methodologies and applicable Client standards to review the existing building and tank farm electrical instrumentation and controls infrastructure and capacity.
The BE Process
For the electrical scope of work on the project, the existing MCC sections were utilized to feed the new electrical loads. BE worked with the Client and site electricians to perform load studies on the existing MCC sections to ensure they could accommodate the new electrical loads. These new loads included 12 new 480V variable frequency drive motors, 10 non-reversing 480V motors with local disconnects and J-O-A switches, 2 new electrical heat trace panels, and a new 480V distribution panel. BE worked with the Client, electrical equipment suppliers, and OEMs to specify and procure the required new electrical equipment. The existing MCC room could not accommodate the new electrical equipment, so a new MCC room was constructed above the existing. The new MCC room houses the 12 new VFDs, 480V 225A distribution panel, third-party provided PLC, and the new heat trace controller panels. Existing site lighting and power distribution panels were evaluated and utilized for the new MCC room HVAC, lighting, and receptacle power distribution.
For the existing building fractionation instrumentation and controls scope of work, there were approximately 350 new I/O points and associated instruments and equipment within the system. This equipment and instrumentation are monitored and controlled within a new third-party furnished PLC, tied into the existing site controls network via redundant fiber optic cabling, and located in the new MCC room. The 12 new VFDs communicate with the new PLC via ethernet cables. Five new field junction boxes and associated homerun cables were fabricated/installed to hardwire the new field devices to the PLC. New instrumentation was specified and procured by both BE and the OEM supplier. The instrumentation was installed on both new and existing tanks and equipment. BE worked closely with the Client, Instrumentation Vendors, and the OEM supplier to ensure the instrumentation was suitable not only for the process conditions, but also suitable for both the new and existing process connections. For the interesterification and mitigation portion of the project, there were approximately 200 new I/O points and associated instruments and equipment. This equipment and instrumentation are monitored and controlled via 8 new panels added to the Client’s existing Ethernet/IP Device Layered Ring (DLR) within the existing tank farm. Again, our EI&C team members worked diligently will all interested parties to ensure complete and seamless instrumentation and controls integration for the new interesterification and mitigation systems.
The BE Result
In summary, Brindley Engineering successfully partnered with our Client to expand their refinery capacity by upgrading the fractionation unit and interesterification systems. BE’s team applied their expertise in electrical instrumentation and controls systems to ensure a seamless transition and optimized integration. Despite the challenges of utilizing both new and existing infrastructure, BE’s thorough evaluations, studies, and collaborative engineering and design efforts with the Client and suppliers led to the effective implementation of the new systems.
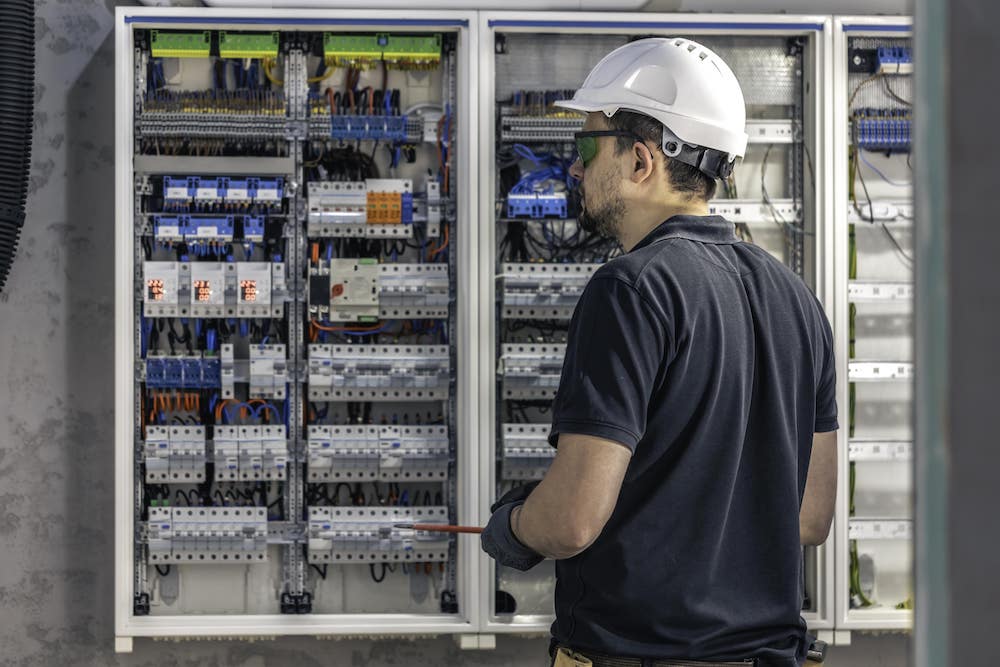
0 Comments