FFS stands for “Fitness-For-Service” and has been an API Recommended Practice 579 since January 2000. By June 2007, it became a Standard jointly developed by API and ASME. The use of FFS has become more prevalent in recent years for Level 3 FFS assessments, but the oil & gas, refining, petrochemical, pulp & paper, food & beverage, and pharmaceutical industries have been utilizing FFS assessments for almost a quarter of a century.
What is FFS?
Fitness-For-Service is a best practice and standard to evaluate the structural integrity of an asset/component containing identified flaws or damage to determine if it is suitable for continued service under a specified time frame. There are many FFS assessment methods use in the many different industries. For the oil & gas and chemical process industries, API 579-1/ASME FFS-1 is commonly used by industry professionals.
API 579-1/ASME FFS-1 defines FFS as “Quantitative engineering evaluations that are performed to demonstrate the structural integrity of an in-service component that may contain a flaw or damage, or that may be operating under a specific condition that might cause a failure.”
Why is FFS trending?
Fitness-For-Service is trending because the methods can be used at every stage of the asset’s life to indicate whether it is fit for its intended service or whether fabrication defects or in-service deterioration threaten its integrity. Over time, pressure equipment is likely to suffer from some form of degradation, also known as a Damage Mechanism, caused by the process environment. If the damage mechanism is identified, an FFS assessment can be determined to find out the future degradation rate and establish the remaining life.
The assessment can save both money and time repairing or replacement equipment. It can also help increase safety, reliability, efficiency, and availability of equipment. It can also be used to optimize maintenance and operation practices and enhance long-term economic performance of the equipment.
Why are FFS assessments important?
Fitness-For-Service is important because it allows the owner to make an informed decision about how the plant continues to operate for years to come. When an assessment is considered, it encourages a higher standard of safety while optimizing maintenance and inspection programs.
The BE process for FFS Assessments
Brindley Engineering has extensive experience in FFS assessments. In the oil & gas and chemical process industries, BE commonly utilizes API 579-1/ASME FFS-1 which covers methodologies for pressure vessels, boiler components, piping systems, and storage tanks where inspection has revealed degradation and flaws in the equipment. FFS is not a one size fits all and each case must be evaluated for the proper assessment procedure to be used. When BE is presented with the scope, it is important BE understands what the client is trying to achieve with an FFS. When BE utilizes API 579-01/ASME FFS-1 assessment procedure, the eight steps detailed in the standard are completed with a systematic method to ensure all required data is collected. FFS assessment standard generally can be broken down into multiple levels, e.g Levels 1, 2 and 3 referenced in API 579-1/ASME FFS-1. Each successive level requires an increasing amount of data, calculations, effort, and cost to arrive at the most accurate results and possible longer equipment lifetime.
FFS can involve multi-disciplinary engineering, additional external resources or personnel, software, and/or numerical techniques such as finite element analysis.
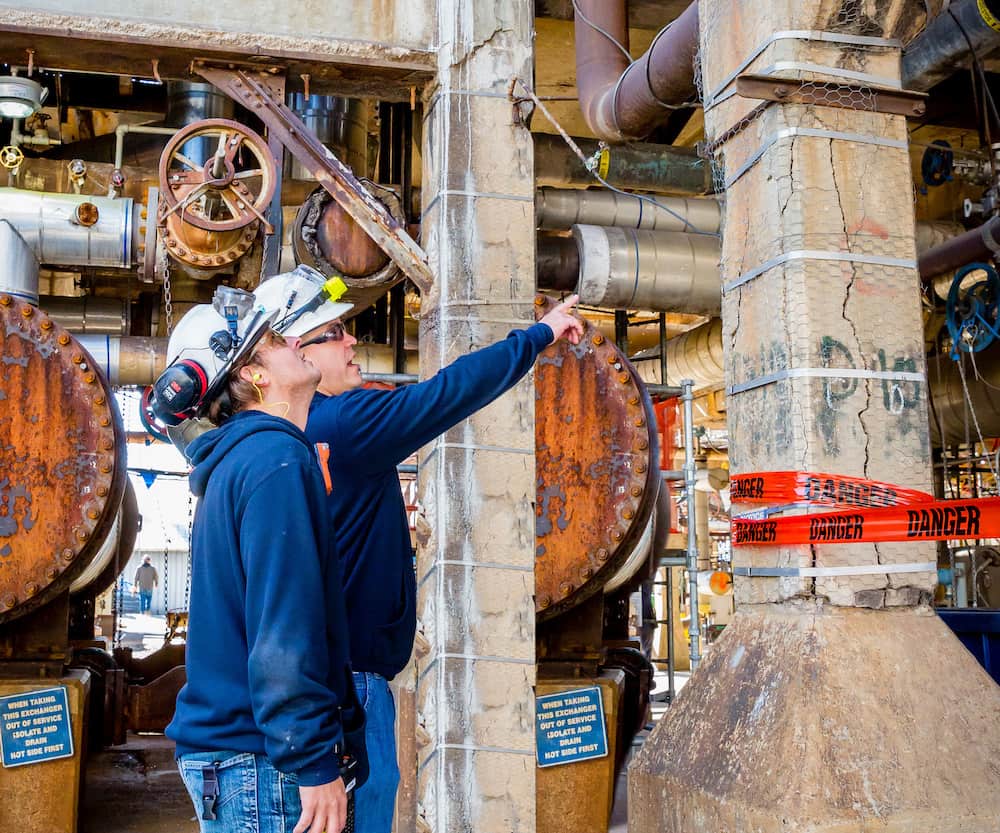
0 Comments